Having the correct type of diamond blades is essential to the performance of your saw. There are a few different types of diamond blades, including circular saw blades, segmented rims, flexible hotdogs, and impregnated diamond wire. These blades are great for cutting different materials, including wood, concrete, plastic, and metal.
Contents
Impregnated diamond wire
Compared to the electroplated diamond wire, impregnated diamond wire is economical. This wire is used in civil, mining, and quarry applications. It can cut various materials, including granite, marble, and stainless steel. It also helps to reduce transportation costs.
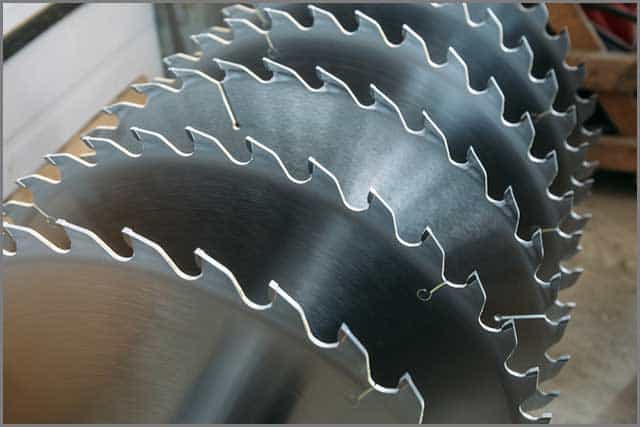
Impregnated diamond wire is designed to provide a smooth and consistently cutting edge. This wire maintains a consistent diameter throughout Diamond Saw Blades life. Impregnated diamond bits are manufactured by placing diamond particles in a carbon mold. These bits are then used to produce diamond saw blades. This process increases the tool’s life by more than double. It is also easier to process various materials with impregnated diamond wire.
Diamond wire saws are ideal for cutting materials that are wet or dry. They are also capable of cutting temperature-sensitive materials and composite materials. They can cut even the thinnest parts. They can also cut iron bars. It is a versatile tool that reduces processing time and waste.
What Are the Different Types of Diamond Blades?
Diamond wire is the newest tool in the processing industry. It is also used in civil applications such as stone processing. It is an economical alternative to deep sawing with large-diameter diamond blades. It can cut virtually any material. The tool requires a power of at least 40 hp to function correctly. It is also simple to operate. It is the most advanced tool for quarrying.
In the present time, more laboratories are investing in diamond wire saws. The properties of this tool include high velocities, high wear resistance, and constant sawing speed. However, it cannot create a radius-free contour cut. It is a more flexible cutting method than other methods. It can be used to cut various materials, including granite, cement, concrete, and even metals.
The manufacturer of impregnated diamond wire is Simond Tools. It was established in the year 1989. It has a vast dealer network and sound infrastructure. It continues to improve its existing products and introduces new diamond materials and manufacturing techniques. It is also a pioneer in the wire saw beads industry in India. It is committed to providing prompt after-sales service.
Flexible hotdog blades
Typically, a flexible hot dog blade has a width of about two to three inches and should be at least six inches long. It should also have a thickness of at least about one-quarter inch. Its cutting edge should be sharp and long enough to cut through a hot dog without slicing through the skin. The width of the blade varies according to the material being cut. Metals are often the preferred material.
A new type of cutting blade is also being introduced to cut designs in food products. This is in addition to the standard cutting functions. The cutting blade handle is usually wood, metal, or plastic and may be attached to the blade at one or more sides. Depending on the design being cut, the handle can be any size.
In the past, hot dog blades have been made of various materials, from stainless steel to aluminum, from plastic to tungsten. These materials can be formed into various shapes, but the cutting blades have traditionally been narrow and hard to hold, which is not a good design for hot dogs. The new blades allow for flexible flexion, which can be helpful when cutting materials such as granite. They can also be made of a rigid material that is easily formed into a curved shape.
The new blades also come in a variety of sizes. The thickness is also variable, depending on the food material cut.
A cutting blade that can cut a nifty little design on the top of a hot dog is an excellent way to demonstrate the function of the blade. In addition to forming a design at the top of the food product, the blade can also cut out ingredients. It can be used to add ingredients to the food product before cooking. Alternatively, it can be used to form a design on the top of a hot dog, then placed in a microwave oven to heat the food product.
While the cutting blade of the present invention may be the first of its kind, several other related innovations could be applied to the production of hot dogs. For example, it can also be used to cut out a design on top of a cold dog, allowing additional ingredients to be incorporated.
Segmented rim
Whether cutting concrete, brick, asphalt, or masonry, segmented-rim diamond blades offer a wide range of benefits and features. They have many advantages over conventional abrasives, such as cutting faster, smoother, and more relaxed. Also, they are designed to provide longer life than bonded abrasives.
There are many different types of segmented-rim diamond blades available. They are designed for different applications, such as cutting soft materials, cutting asphalt, and cutting green concrete. They are also available in a variety of sizes. They are also available for demolition, roadway construction, and more.
Unlike bonded abrasives, these blades can be used wet or dry, which improves their longevity. They are also engineered with gullets or slots to help keep the blade cool. These slots are designed to prevent chipping, which helps ensure a smooth cutting action. They also help reduce noise and dust generation, which improves their performance.
Diamond blades are made from high-quality steel, which helps them withstand high pressures. They also have a metal-bonded segment that holds diamond crystals, giving them a sharp cutting edge. They are designed to last longer than bonded abrasives, which helps to make them the choice of professionals.
Segmented rim diamond blades are the best choice when cutting concrete, brick, or masonry. They provide the fastest cutting, a smooth finish, and the ability to exhaust debris, which improves their longevity. They also offer the highest degree of cut depth.
Segmented rim diamond blades can be used in many applications, including cutting green concrete, straight asphalt cutting, demolition, and roadway construction. They are also available in various sizes, ranging from 6 inches to 36 inches. They also come in three rim types: a continuous rim, an undercut rim, and a segmented rim. They can be purchased online or at any authorized Makita dealer. They also come with free overnight shipping.
Segmented rim diamond blades come in various sizes and designs, and they are available for wet and dry cutting. They are designed to provide faster cutting, longer life, and the ability to use them in various situations.
Circular saw blades
Choosing the right circular diamond saw blade is crucial to the performance and productivity of natural stone sawing. The blade’s tip and segment thickness must be chosen correctly to provide adequate life and a high cutting speed. It is also essential to select a segment matrix/diamond composition that is based on the properties of the rock being cut.
A finite element method can be used to study the dynamic behavior of the diamond saw blade. The blade’s natural frequencies are used to update the FE model. It is essential to separate the saw’s operational speed from the blade’s natural frequencies to avoid structural resonance.
In addition, it is also essential to examine the energy consumption of the saw blade. The energy consumption was determined through an experimental study. It was found that energy consumption increased with the cutting speed. The Fn force was higher than the Ft force. This effect is attributed to the increased circular velocity. Similarly, the tangential force is reduced as the circular velocity increases.
Another critical area of research is developing a novel cutting power model. This model provides the optimal separation of the FEA results and the operational speed. The results should provide improved designs for saw blades.
The blade models were created with ANSYS software. They were then modified to simulate sawing machine clamping. Later, they were updated with free-free boundary conditions. The disc segment mesh was created using 43146 nodes.
The diamond saw blade was then tested to extract the natural frequencies of the blade. A three-directional dynamometer was used for the cutting force. The FEA model was then updated using the measured frequencies. The resultant was found to be around 155 N/mm and 360 N/mm. Two thin strings also suspended the blade to simulate a free-free boundary condition.
The results were used to construct a new model for estimating SE and SW of circular diamond saw blades. It was determined that the maximum resultant occurred when the specific material removal rate Qw’ was 800 mm2/s.